Troubleshooting Guide
The most common issues can be resolved quickly and simply without the need to return your Perfect Descent Auto Belay to an authorized service center. Immediately remove from use any unit that is observed to be operating improperly or outside of stated limits and quarantine the device until such a time that the issue can be identified and resolved.
Lanyard is retracting slowly or does not retract completely
Check the lanyard for excessive wear and fuzz
As the lanyard wears, it can develop excess fuzz that creates friction between the lanyard and nozzle. This friction can slow retraction and, in some cases, may prevent the lanyard from fully retracting. Check the condition of your lanyard and replace if excessively worn.
Check for internal contaminants
Excessive debris from worn lanyards and heavy chalk use may slow retraction speed. Remove the lanyard and use a high-powered vacuum to remove excessive buildup. Never blow compressed air into the unit.
Check retraction force
Perfect Descent uses a redundant twin-spring retraction system. Test the retraction force using these guidelines to determine if both retraction springs are functional.
Check your tag line
If you notice slow or incomplete retraction when using a tag line to retract the lanyard for temporary or overnight storage, the weight of the tag line could be your problem. Perfect Descent auto belays are design to exert minimal forces on the climber, and it doesn’t take much weight to slow retraction. Always use small diameter and lightweight tag lines.
Check lanyard spooling
Occasionally, the lanyard can become twisted inside the unit. This usually occurs when a Speed Drive lanyard retracts unguided back into the device. To remove any twists in the line, slowly extract the entire lanyard, and using a lightweight tag line, slowly guide the lanyard back into the fully retracted position.
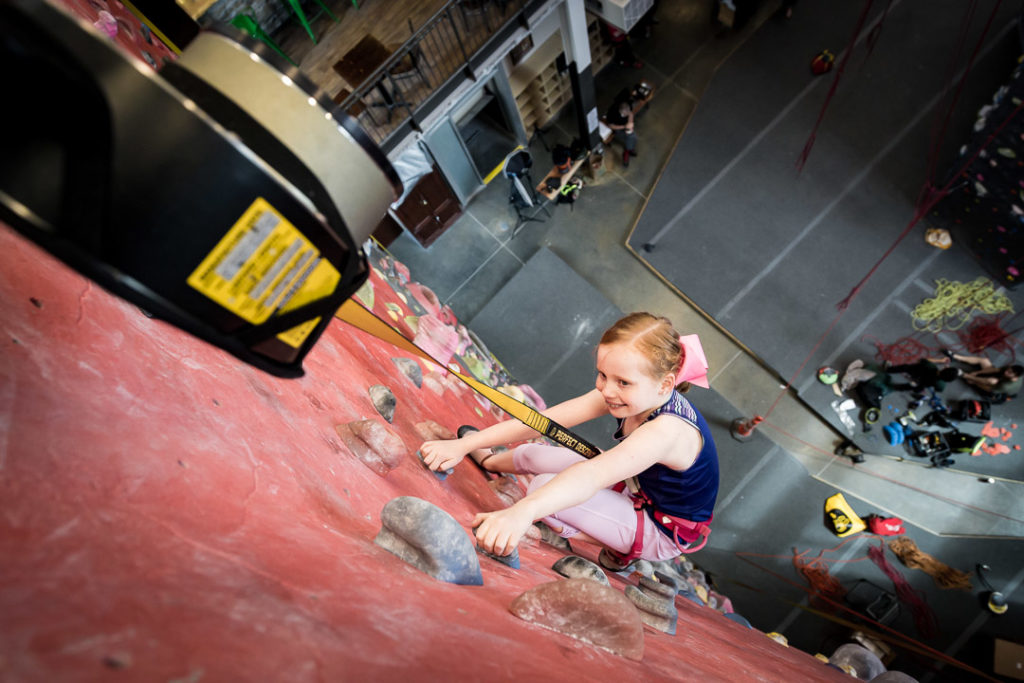
Auto belay is making noises
It sounds like a tape measure spooling
It is common to hear a sound similar to a tape measure spooling when the device is retracting. This is the retraction spring coiling inside the unit and is normal.
One unit is louder than another
Perfect Descents are among the quietest of all auto belays. Decibel levels emitted during use can vary from unit to unit and can be more or less amplified by their position and attachment to a structure.
The unit is making a pronounced ratcheting noise
A pronounced ratcheting or grinding noise can be an indication of internal damage or excessive wear. Stop use immediately and quarantine the device until it can be inspected by an authorized technician. You can hear an example of a unit requiring immediate attention here.
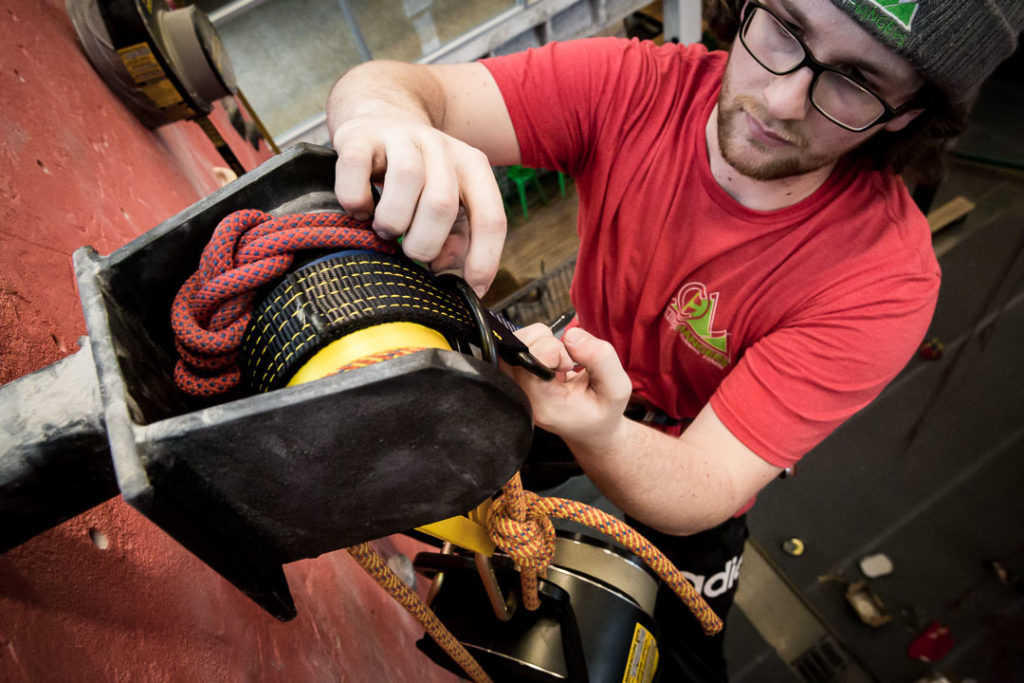
Descent is choppy or faster than normal
Check lanyard spooling
The lanyard may have spooled improperly. Use a lightweight tag line to fully retract the lanyard. Once retracted, pull (extract) the entire length of lanyard from the unit using the tagline.
Check lanyard length
Using a lanyard that is considerably longer than the mounted height of the unit can cause improper spooling. Make sure to install units with a lanyard length that most closely matches the intended mounting height. Avoid using long lanyards on short walls. Follow the steps for checking lanyard spooling if descent is choppy or faster than normal. Perform the lanyard spooling check before each operating day on units with persistent choppiness. This is especially important when the auto belay is mounted at heights below 5.5m (18ft).
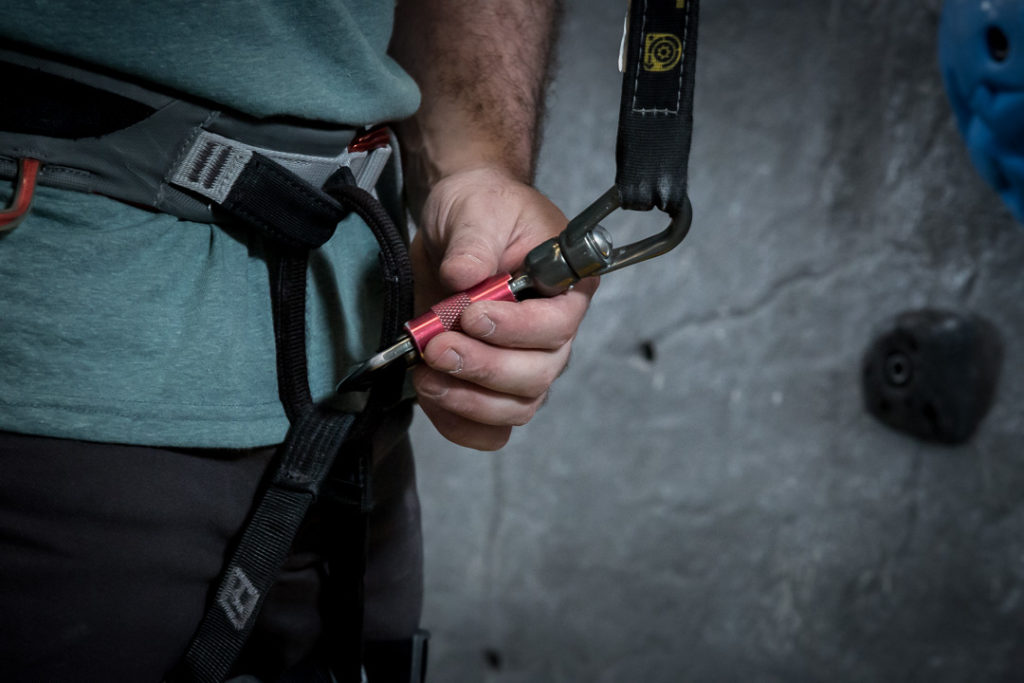
Carabiner gate is not functioning properly
Carabiner gate fails to fully close and/or lock
Inspect carabiner for deformation or other damage. Clean all loose chalk and debris from the carabiner using a clean, damp cloth. For heavily soiled carabiners, gently washing in warm water with a mild detergent may be needed. Use compressed air to remove hard-to-reach debris. Carefully lubricate the gate, hinge, swivel, and locking collar with a light machine oil such as 3-IN-ONE or Cam-Lube. Do not allow the lubricant to contact the nylon lanyard as this may cause damage. Activate the locking gate and swivel several times to assist lubricant penetration. Test the gate and if still not functioning properly, replace the lanyard.